From technical committee to competence network
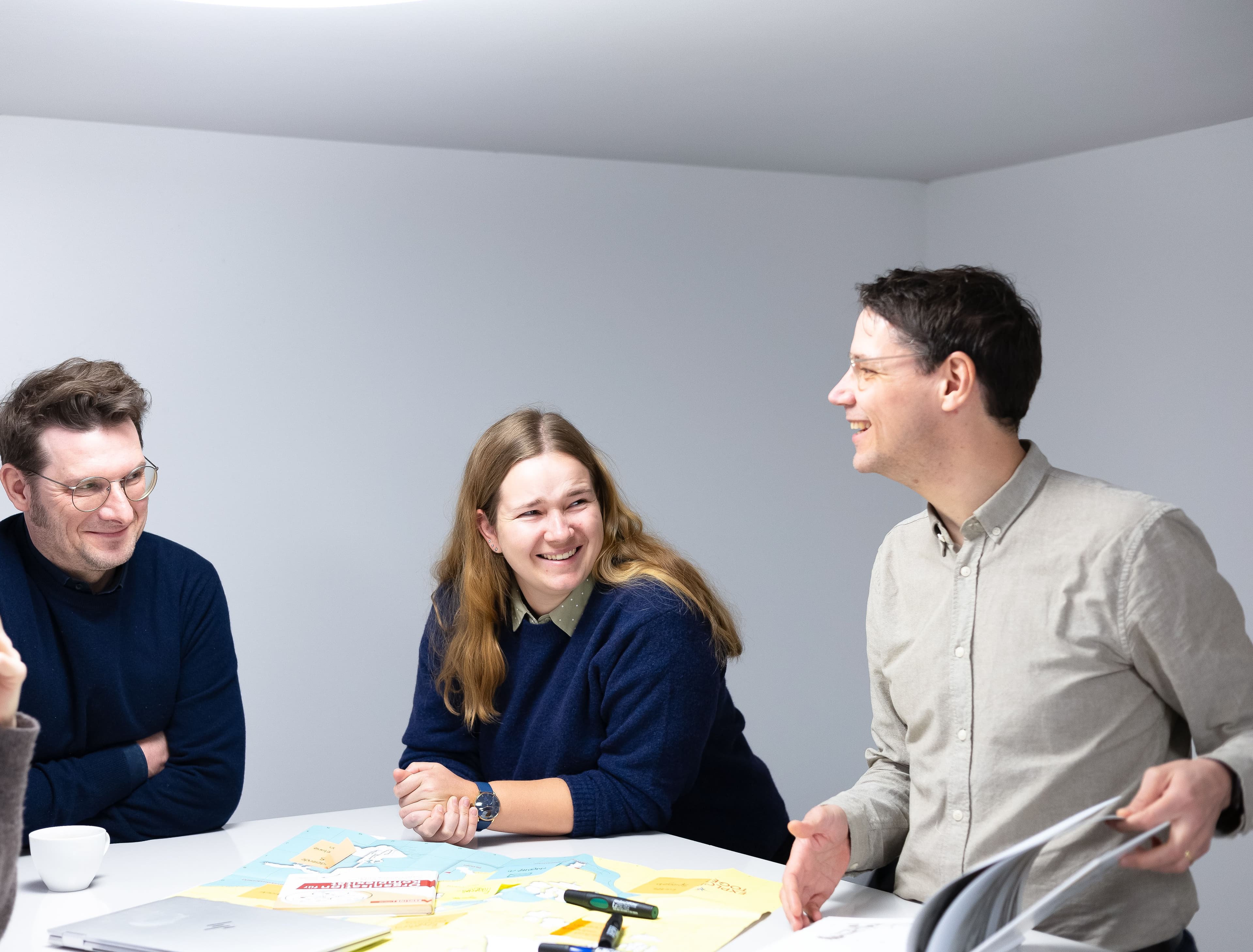
‘What did you learn in this process?’ – Environmental engineer Ulla Hartmann doesn’t hesitate for a second: ‘As with many things, it’s all about getting started. The new heat pumps network will evolve over time and will never truly be “finished”. I’ve already learnt an incredible amount about heat pumps from my colleagues.’ Ulla’s insight goes to the heart of a transformation that is also affecting our industry: Merely possessing specialist knowledge is no longer enough. It’s only through exchange in ongoing projects and sharing experiences from other projects that a real expert network can be created – one that remains capable of learning and continuously adapts to new challenges.
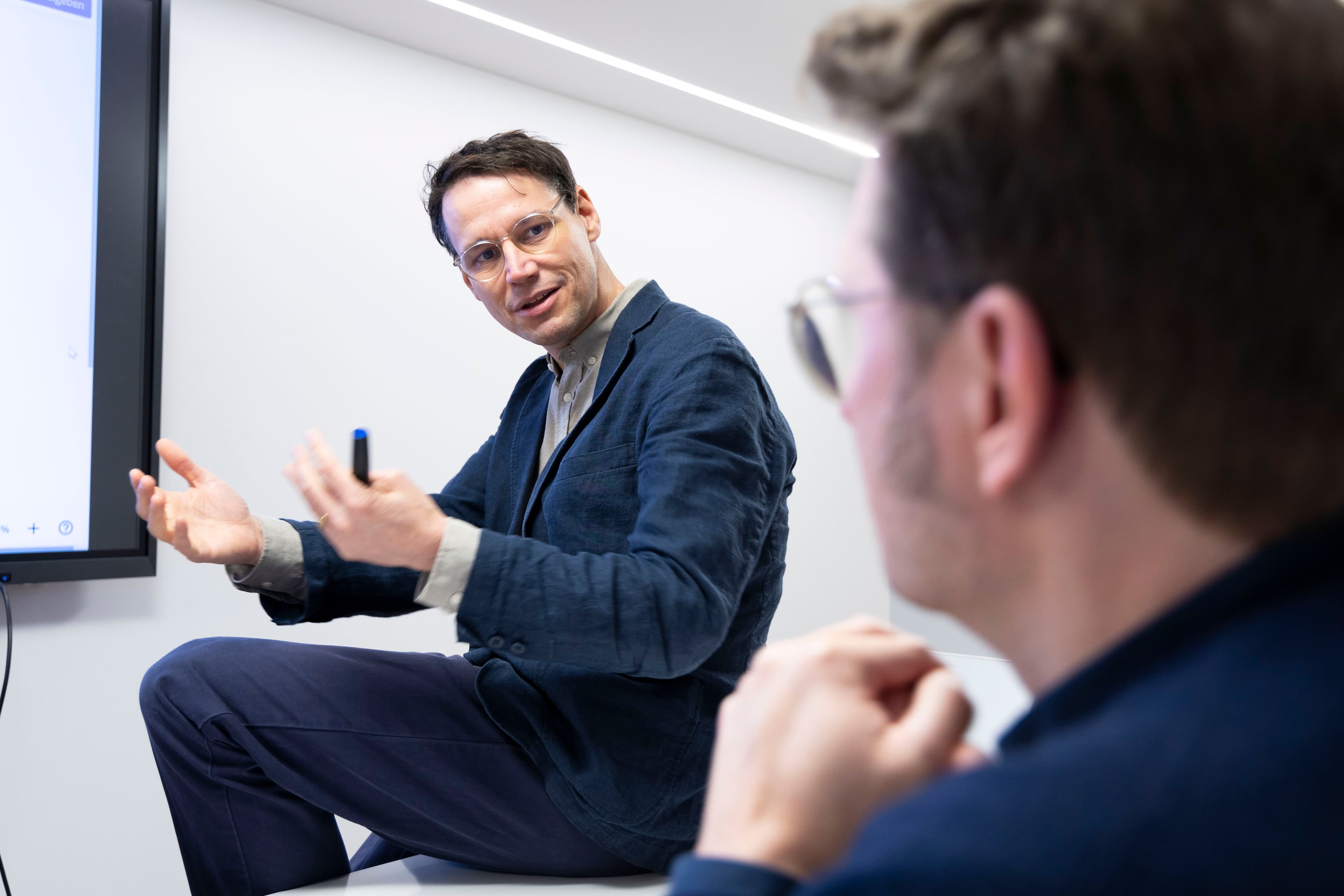
From isolated specialist knowledge to interlinked expertise
As the French philosopher Michel Foucault once noted, ‘Knowledge is power’. But what does this mean in times of rapid technological development? Knowledge was once regarded as a fixed quantity: the sum of collected, archived and controlled information. The sheer quantity of knowledge was regarded as guarantee of quality. In this mindset, we formed a technical committee in 2012, which was tasked with defining and complying with quality standards and regulations. However, knowledge is changing faster than ever and limiting our knowledge to just a few individuals is no longer sufficient. Alongside the company’s growth and an increasingly broad range of services, it became apparent that we needed a new structure that allows the previous technical committee to perform its key role in a new form.
The transformation from a technical committee to a “competence network” highlights a change that has been happening for a while now: we increasingly collaborate within network structures – bringing people with the same concerns but different perspectives and backgrounds together to actively connect, share and develop their expertise. ‘Admittedly, I needed some time at first to break away from the idea of the technical committee and understand the notion of the competence network,’ adds Jens Schmidt, a process and environmental engineer and a member of the technical committee since 2012. Today, he notes that this transformation was a logical and necessary step. ‘Especially because we took this step a long time ago in other areas at TBF: The technical committee has followed the trend, so to speak.’
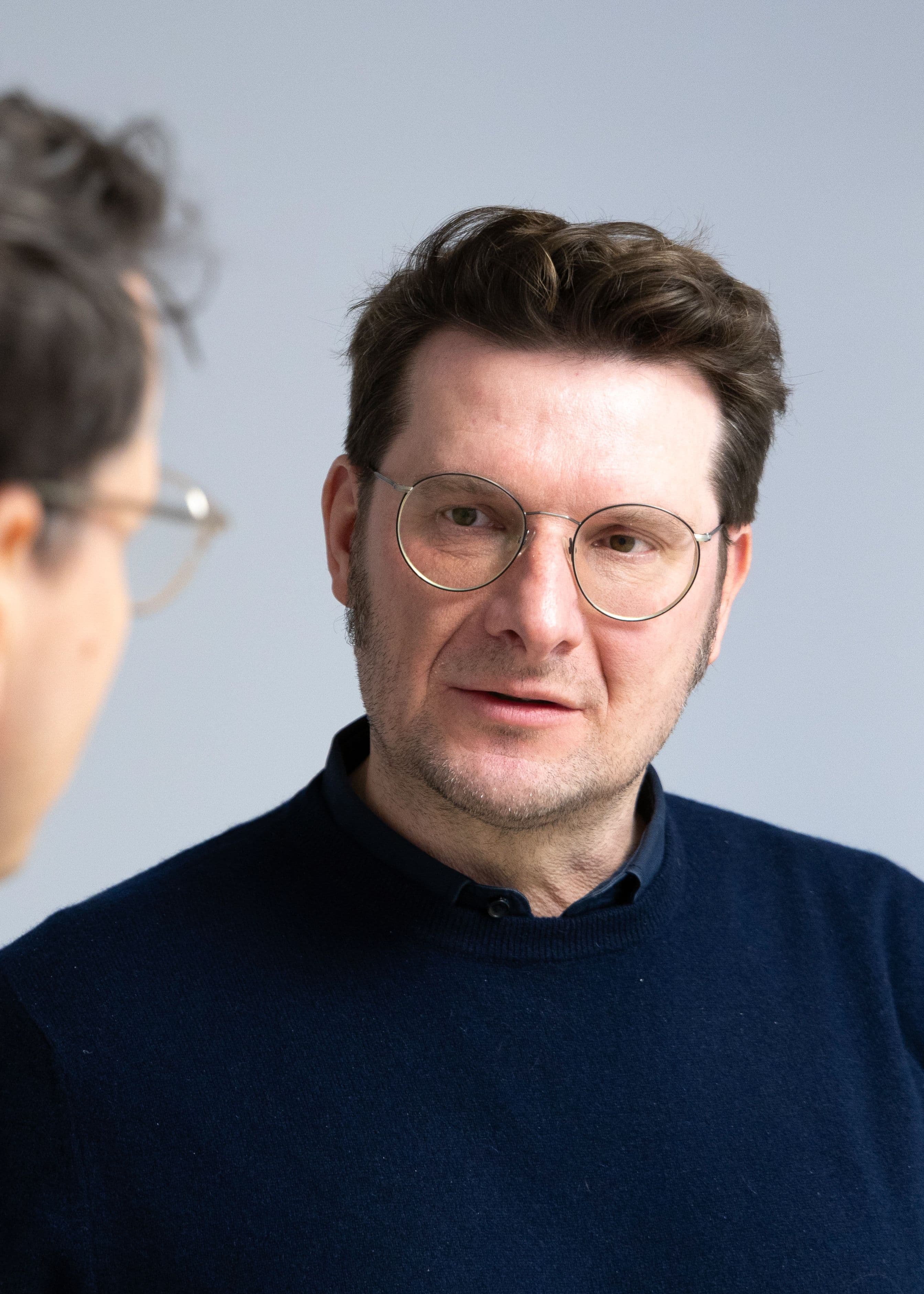
Quality becomes a matter of culture
Wide network participation enables a new approach to quality through a shared sense of responsibility and intensive dialogue. Quality becomes a dynamic product of negotiating needs and expectations. This is reflected above all in the growing complexity of the projects: ‘Our projects are unique – we’re not manufacturing chair legs,’ adds civil engineer Christian Hengemühl. ‘We are aware of the great responsibility we bear in our projects. The challenge is not only to build expertise, but to make expertise available as a resource across teams and projects,’ explains Christian – turning knowledge into skills. This new understanding of quality requires us to break away from the notion of quality as something stable and measurable. This is challenging, as we lose the sense of quality “control” as we know it.
Communication is a key factor in this process: we all make mistakes, have questions or feel insecure about particular topics. These imperfections fuel the learning process for everyone involved. As such, quality has a lot to do with our culture of collaboration: do we share our mistakes, to learn from each other and improve together? This requires mutual trust and a willingness to self-reflect. Quality becomes a shared and dynamic objective as well as an attitude. ‘By embodying quality as an attitude, we develop a working environment that promotes diverse dialogue,’ adds Jens.
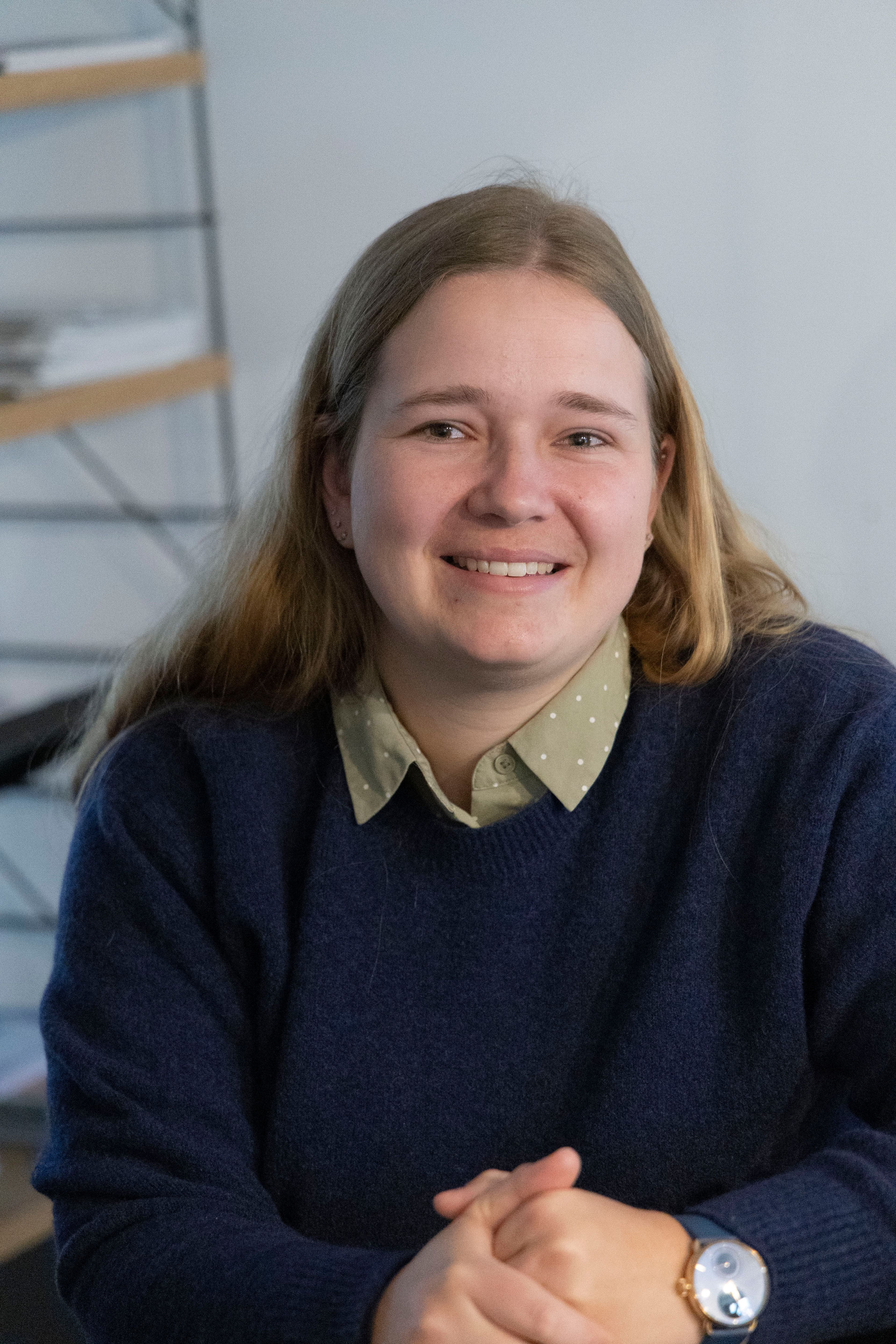
Case study: the heat pumps network
That brings us back to Ulla and the heat pumps. Because heat pumps play a central role in a growing number of projects, a “heat pump network” was created. Ulla, who co-founded the network, describes the process as follows: ‘we brought together people with specific skills and interests in the field, encouraged them to share responsibilities and structure sub-topics. This makes knowledge accessible and comprehensible to everyone.’
A network like this is more than just a source of knowledge – it promotes collaboration and the exchange of good practice, enabling all participants to learn from each other. Such specialist networks are constantly emerging – and can be dissolved again when they are no longer relevant.
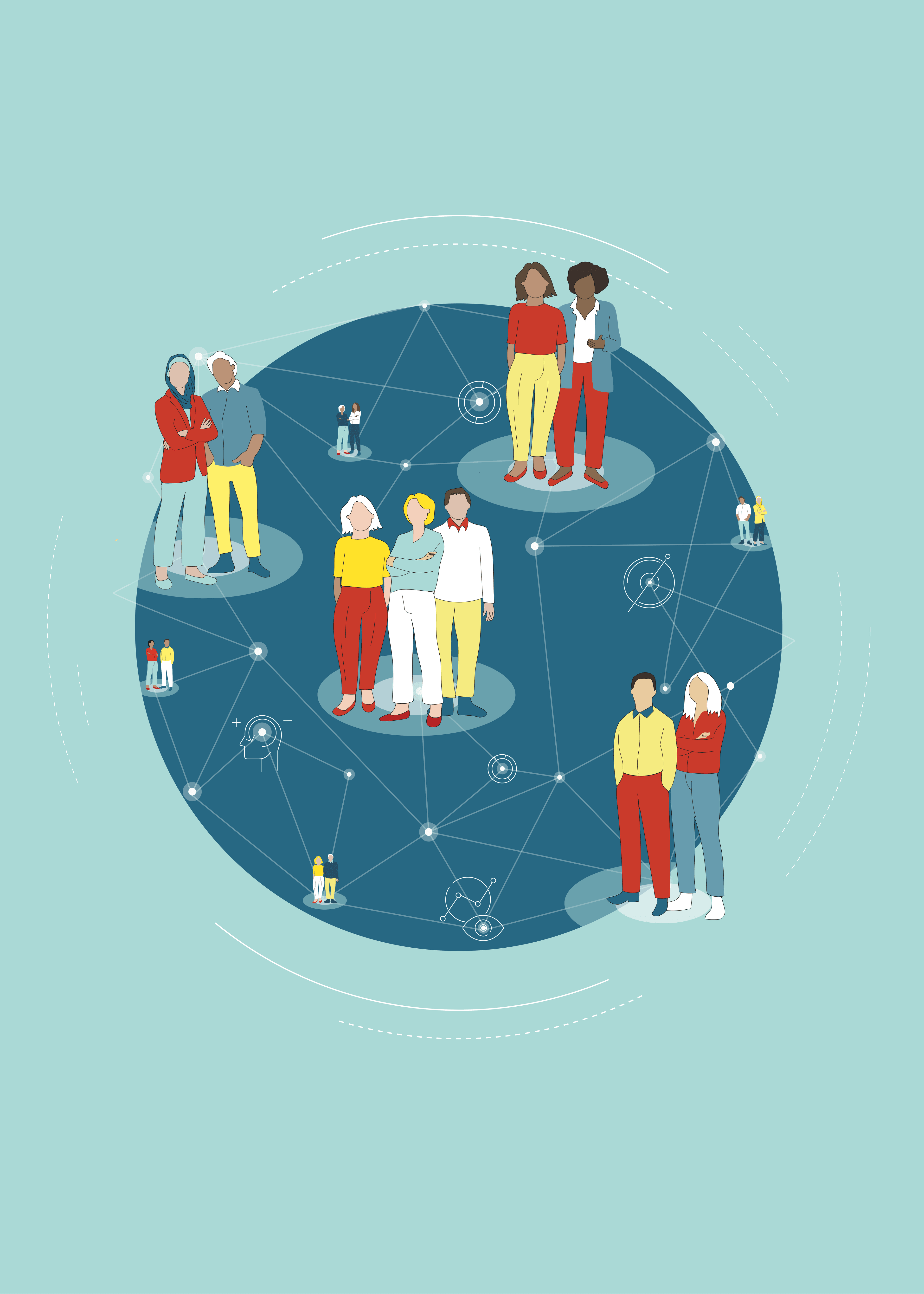
“Self-organised networks create a remarkable dynamic.”
Andreas Münzmay
Andreas Münzmay, a process engineer focusing on thermal waste recycling and a driving force of the technical committee since 2017, describes this as follows: ‘What excites me is the dynamic that comes from self-organised networks. Everyone’s unique skills are in demand. By allowing our employees to organise themselves, no one has to wait for the committee to take on a new topic.’ The specialist networks thus become true communities of practice. As a result, their activities themselves are no longer handled by a central body – a clear change from before.
It’s important to bear in mind that not all professionals are born organisers or networkers. A coordination network has been set up to ensure relevant topics are covered, avoid redundancy and facilitate communication. At the same time, the team ensures that long-term topics such as calculation tools and standards are managed efficiently and securely. In addition to the members of the original technical committee, this coordination network includes professionals specialising in communication and collaboration. Andreas weighs in: ‘As an “old-timer”, I’m very happy and grateful for their support. Working with the new team members helps me realise my own habits and it shows me the value of seeing things from a different perspective.’